ALÜMİNYUM VE ALAŞIMLARI İÇİN YÜKSEK KALİTEDE Cr +3 KROMATLAMA PROSESİ
Hazırlayan : Ferit SATICIOĞLU – DEDE KİMYA
Son 30 yıldır Cr (VI) kullanımından doğan tehlike, çeşitli endüstri ve çevrecilerin ilgi odağı olmuştur. Kaplama yüzeyinden çıkan süzülebilir kalıntılar ve kaplama solüsyonlarından havaya karışan asılı taneciklerin oluşturduğu zararları önlemek amacıyla bir takım yönetmelikler oluşturulmuştur. Yapılan düzenlemeler daha sonra otomobil parçaları için oluşturulan ELV yönergelerine de yansıtılmıştır. Bu yönerge 2006 ortalarında son halini almıştır. Metal kaplama teknolojisi, yönergede öngörülen çinko ve çinko alaşımlarına uygulanan Cr(VI) içermeyen kimyasal dönüşüm kaplaması ile ilgili hususları karşılamaktadır. Bu yeni kaplama sistemleri Cr(VI) dan elde edilen performansı fazlasıyla yerine getirebilmektedir.
Aynı teknolojiyle benzer beklentiler alüminyum için elde edilememiştir. Alüminyum için kimyasal dönüşüm kaplaması, iki temel özelliği karşılamak zorundadır.
1) Çıplak korozyon direnci (dönüşüm kaplaması üzerine herhangi bir boya veya başka bir uygulama yapılmamış olması)
2) Dönüşüm kaplaması üzerine, boya veya diğer uygulamalar için iyi bir yüzey yapışması
Endüstriyel beklentiler bu tip ölçülebilir özellikleri kapsamaktadır ve bunun için oluşturulan düzenlemeler, Cr(VI) tip kaplamaların performansı baz alınarak oluşturulmuştur. En popüler olanları MIL 5541 ve MIL 81706 dır.
10 yılı aşkındır krom 6 içermeyen kimyasal film geliştirilmesi için birçok girişimler yapılmıştır. Bunlardan bazılarının yapışma özellikleri iyi olup, alışımlar üzerinde çıplak korozyon direnci ticari olarak kabul edilebilir olmamıştır. Bakır zengini alaşımlar özellikle 2024-t3 ve 2219-t 87 gibileri bu sistemlere uygunluk arz etmemektedir.
Son zamanlarda US denizcilik tarafından yeni bir proses patenti alındı. Bu proses düşük seviye Cr(III) içeriyordu ve tamamıyla Cr(VI) dan uzaklaştırılmıştı. Böylece bu ürünün Cr(VI) yerine ticari olarak kullanılabileceği ispatlanmış oldu. Cr(VI) kanserojen özellik gösterirken krom III ün zararlı olmadığı hem düzenleyiciler ve ilgili sağlık kuruluşları tarafından açıklanmıştır. Proses ticari olarak SurTec 650-ChromitAL adıyla piyasada mevcuttur. Daldırma, spreyleme ve fırçalama yöntemleriyle uygulama yapılabilmektedir.
Alüminyum ve alaşımları için yüksek kalitede üç değerlikli kromatlama prosesi.
Boyanmamış yüzey üzerine mükemmel korozyon dayanımı sağlar ve organik kaplamaların yapışma gücünü artırır. İşlem görmemiş ve eloksallanmış alüminyum uygulamaları mevcuttur.
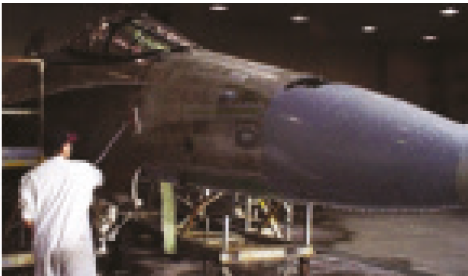
Elektriksel temas direnci:
Elektriksel ve elektronik araçlar kesintisiz bağlantı için, yüzeylerde düşük elektrik direnci istemektedir (topraklama ve EMF direncine karşı)
5541 class III standardını karşılayan Cr(VI) pasivasyon tabakası bu özelliği sağlamaktadır. Bu talepleri karşılamak için pasive edilmiş yüzey, nötral tuz sisine 168 saat maruz bırakılıp yüzeydeki kontakt direnci ölçülmelidir. Korozyonda artış görülmesi, kontakt direncini maksimum izin verilebilir limitler dışına çıkartır.
Her ne kadar pasive olmuş yüzeyde, krom içermeyen sistemlerde aynı özelliği sağlasada, çıplak korozyon dirençleri tuz testi sisinde 24-72 saatten sonra başarısız olmaktadırlar.
Tablo 4 Mil DTL 81706 (Şekil 1)’e göre ChromitAL TCP nin kontakt direncini göstermektedir. Krom VI ile karşılaştırıldığında, 168 saat tuz testi sisinden sonra daha düşük direnç görülmektedir.
Kaplı Yüzeyler
Alüminyum üzerine astar boya, boyama ve vernikleme gibi birkaç önemli kaplama uygulaması mevcuttur. Dönüşüm kaplamaları bu tür kaplamalar için iyi yapışma ortamı sağlamasına rağmen, zarar gören boya tabaka alt bölgeleri için de koruma sağlar.
Krom (VI) içermeyen bu tür sistemleri değerlendirmek amacıyla birkaç test yöntemi uygulanmaktadır. Çeşitli alaşımlı paneller üzerine boya uygulamasından sonra, yüzey çapraz şekilde çizilir ve panel aşağıdaki testlere tabi tutulup değerlendirme yapılır.
Kuru şerit yapışması
Islak şerit yapışması
Nötral tuz sisi, 3000 saat
SO2 tuz sisi 500 saat
GM 9540 periyodik test 120 periyodik
Lif korozyonu
Deniz suyu uygulaması, 4, 8, 12 ay
Tüm bu testlerde chromitAL TCP sarı Cr(6) kimyasal film performansına eşdeğer çıkmış yahut daha fazlasını karşılamıştır. Lif korozyon testi uygulaması boyalı yüzeyler için en önemli olanıdır. Bu testte su bazlı veya solüsyon bazlı boya ve astar boya kaplamalı farklı alaşımlı paneller X şeklinde çizildi ve aşağıdaki gibi test edilip değerlendirildi.
1- Parça 1 saat kadar HCl buharına maruz bırakıldı ve sonra
2- 40 °C % 80 nemli ortamda 1000 saat bırakıldı.
İşaretli bölgedeki korozyon boyanın altında gerçekleştiği için korozyon büyümesi başlangıçta görülmez. Sonuçta korozyon büyümeye başlar ve yüzeye çıkar. Bu durum yapışma gücünü etkisiz hale getirir ve ana metale zarar vermeye başlar. Test sonucunda korozyonun varlığını panelin yarısından, boyanın boya sökücü ile soyulmasıyla ölçülür. Maruz kalan çizgi bölgeleri incelenir. X işaretinin olduğu bölgede her bacağa 60 kare içeren bir şablon yerleştirilir. Çiziklerin olmadığı kareler sayılır ve performansı 0-120 arasında değerlendirilir.
Şekil 2 korozyon testinden sonra soyulmuş paneli gösterir. Tablo 5 test edilen panelleri karşılaştırır. 2024-T3 alaşımları üzerine ChromitAL TCP, Cr(6) ve diğer kromsuz sistemlerden daha iyi performans göstermiştir.
Uygulamalar
Yeni krom (VI) sız ChromiatAL TCP çok yönlü bir sistemdir. Yüksek bakır ve silikon içeren alaşımlar üzerinde çıplak korozyon testi için I. sınıf ve düşük korozyon direnci için III. sınıf özelliği eş zamanlı olarak karşılamaktadır. Boya yapışması için mükemmel bir yüzey oluşturmaktadır ve eloksallanmış alüminyum için düşük sıcaklıklı lak (sealer) etkisi göstermektedir. Kadmiyum, kalay-çinko, çinko-nikel kaplamalarının önişlemleri için de uygulama alanı mevcuttur..
Aşağıdaki endüstrilerde alüminyum uygulaması yapılmaktadır.
Uzay araçları-hava araçları, Otomotiv tekerlekleri, Bisiklet tasarımcıları, Elektrikli ve elektronik ekipmanlar, Frekans yönlendiricileri, Denizcilik endüstrisi, Mimarlık Proses ELV, RoHS, WEE yönetmeliklerini karşılamaktadır ve ticari olarak dünya genelinde mevcuttur.